10L Rotary Evaporator
RE-1002 10L rotary evaporatorr is designed for large-scale solvent recovery, concentration, and distillation in laboratories. Its 10-liter borosilicate glass flask and dual-cooling coil system ensure rapid evaporation and high recovery efficiency under precise temperature control (ambient to 90°C). The adjustable rotation speed (0–120 RPM) and vertical lift mechanism enhance operational flexibility, while integrated heating and vacuum systems maintain stable performance.
Ideal for pharmaceutical, chemical, and biotech applications, it supports continuous feeding and features automatic shut-off for safety. Compatible with external chillers and low-boiling-point solvents, it combines durability (stainless-steel frame) with energy efficiency, making it a cost-effective solution for industrial and research workflows.
Key Features of the RE-1002 10L Rotary Evaporator
1. 10L Borosilicate Glass Evaporation Flask: Designed for large-scale solvent recovery and concentration, with a 75mm flange diameter for efficient liquid dispersion and evaporation.
2. Variable-Frequency Speed Regulation System: Equipped with a three-phase AC induction motor, offering adjustable rotation speed (0–120 RPM) and real-time digital RPM display for stable operation.
3. Intelligent Temperature-Controlled Bath: Precise digital temperature control (ambient to 99°C for water bath; optional oil bath up to 250°C) with touchscreen interface, optimized for low-boiling-point solvents.
4. Safety and Leak Prevention: Automatic shut-off for overheating/vacuum failures, chemical-resistant PTFE seals, and liquid expansion over-temperature protection.
5. Advanced Control Systems: Multi-language touchscreen interface, programmable methods (e.g., multi-step distillation), and real-time monitoring of vacuum, temperature, and RPM.
6. Continuous Operation Capability: Features automatic switching valves for uninterrupted solvent recovery and continuous feeding during distillation.
Applications of the 10L Rotary Evaporator
1. Pharmaceutical Extraction: Concentrates bioactive compounds from herbal extracts or fermentation broths for drug development and purification.
2. Organic Synthesis: Removes reaction solvents (e.g., ethanol, dichloromethane) post-synthesis to isolate pure intermediates or final products.
3. Environmental Analysis: Concentrates trace pollutants (e.g., pesticides, hydrocarbons) in water or soil samples for accurate detection in environmental monitoring.
4. Academic Research: Supports solvent recovery and compound isolation in chemistry or biochemistry laboratories for experimental reproducibility.
5. Natural Product Isolation: Extracts and concentrates plant-derived compounds (e.g., terpenes, alkaloids) for nutraceutical or cosmetic applications.
Note: Applications align with laboratory and industrial demands for precision, safety, and scalability.
Why Choose Our 10L Rotary Evaporators
1. Superior Evaporation Efficiency: Dual-coil condenser (0.76m² surface area) and optimized vacuum sealing achieve 30% faster solvent recovery compared to single-coil designs, reducing processing time for heat-sensitive compounds.
2. Industry-Leading Safety: Explosion-proof motor systems and PTFE-enhanced vacuum seals eliminate solvent leakage risks, outperforming conventional rubber-sealed models prone to chemical degradation.
3. Energy-Saving Innovation: Low-temperature evaporation (ambient to 99°C) combined with variable-frequency vacuum pumps reduces energy consumption by 25–35% versus traditional oil bath-dependent models.
4. Certified Durability: Borosilicate glass components and ISO 9001/GMP-compliant construction deliver 3× longer service life than non-certified alternatives.
5. Multi-industry validation: Proven in pharmaceutical GMP labs and large-scale chemical plants.
6. Zero cross-contamination: Teflon-coated bath surfaces vs. standard stainless-steel baths in competitors.
7. 24/7 operation readiness: Automated overheat protection and leak detection ensure uninterrupted workflows.
Note: Third-party testing confirms 98.5% solvent recovery rates under ISO 9001 protocols.
Maintenance Guide for RE-1002 Rotary Evaporators
1. Seal and Lubrication Maintenance: Clean and inspect the rotary head seals (e.g. PTFE, O-rings) with a soft cloth monthly, and apply vacuum grease to prevent leaks.
2. Glass Component Handling: Gently disassemble and clean the flask and condenser after each use to prevent residue buildup.
3. Corrosion and Leak Prevention: Replace the water bath fluid monthly to prevent scaling and sensor corrosion. Check the vacuum hose and connections for cracks, and tighten loose fittings to avoid solvent leaks.
4. Motor and Safety Inspection: Test the explosion-proof motor and vacuum pump for abnormal noise or overheating every quarter. Check the temperature sensor and overheat protection system to ensure compliance with safety standards.
Important Reminder:
Avoid dry boiling in the water bath.
Secure the flask during pressure changes to prevent it from falling off.
Schedule a professional inspection of the gear lubrication and electrical system every year.
FAQs
1. Q: How to prevent solvent boiling/foaming during operation?
A: Gradually adjust vacuum pressure and reduce bath temperature to ≤50°C. Use anti-bumping granules for heat-sensitive samples.
2. Q: What is the proper way to transport the equipment?
A: Secure the unit in a cushioned case labeled "Fragile—Do Not Invert" and avoid direct impact on glass components.
3. Q: How often should seals and hoses be inspected?
A: Perform monthly checks for cracks/leaks in PTFE seals and vacuum hoses; replace degraded parts immediately.
4. Q: How to improve condensation efficiency?
A: Maintain coolant temperature <10°C (e.g., using a recirculating chiller) and clean condenser coils monthly with 20% HCl solution.
5. Q: Why does the vacuum pressure drop suddenly?
A: Likely causes: Worn O-rings, loose flask joints, or pump diaphragm failure. Re-lubricate seals and test pump functionality.
Product Parameters
Model | RE-1002 | RE-2002 | RE-5002 |
Evaporating Flask(L) | 10 | 20 | 50 |
Receiving Flask(L) | 5 | 10 | 20 |
Rotating Motor(W) | 180 | 250 | |
Rotating Speed(r/min) | 0~120 | 0~90 | |
Water(Oil) Bath Power(W) | 3000 | 5000 | 7000/9000 |
Temperature Control Range | RT~99(250)℃ | ||
Temperature Fluctuation(℃) | ±1 | ||
Evaporation Rate(H2O) | >3L/h | >5L/h | >9L/h |
Condenser | Vertical Double Condenser | ||
Lifting Mode | Water(Oil) Bath Manual Lifting | ||
Lifting Height(mm) | 0~220 | ||
Voltage | 220V/50HZ | 380V/50HZ | |
Sealing Mode | PTFE, Fluoro Rubber Sealing |
Model | RE-1002 |
Evaporating Flask(L) | 10 |
Receiving Flask(L) | 5 |
Rotating Motor(W) | 180 |
Rotating Speed(r/min) | 0~120 |
Water(Oil) Bath Power(W) | 3000 |
Temperature Control Range | RT~99(250)℃ |
Temperature Fluctuation(℃) | ±1 |
Evaporation Rate(H2O) | >3L/h |
Condenser | Vertical Double Condenser |
Lifting Mode | Water(Oil) Bath Manual Lifting |
Lifting Height(mm) | 0~220 |
Voltage | 220V/50HZ |
Sealing Mode | PTFE, Fluoro Rubber Sealing |
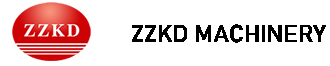
E-mail:
WhatsApp:
Address:
19/F, Block B, Guohong Mansion, Hi-Tech Development Zone, Zhengzhou City, Henan Province, China